Six Practical Questions for Choosing the Right Adhesive
The following questions will help you narrow down your adhesive selection:
What materials need to be bonded?
Structural adhesives work by bonding to the surfaces of components, so it’s crucial to understand the specific materials and conditions of those surfaces. For metals, will the adhesive be applied to raw metal, or is there paint or a coating? For plastics, which resin base is being used? Are there any release agents remaining on the surfaces?
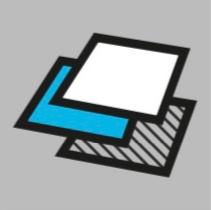
What is the final cure time required?
The selected structural adhesive should have a cure time sufficient to allow mixing, application, and assembly of the bonded parts. Smaller assemblies or production processes with short cycle times may benefit from high-speed curing adhesives that cure in five minutes or less, while larger assemblies requiring alignment and holding may need cure times exceeding 20 minutes.
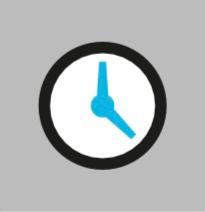
What surface preparation is needed?
Structural adhesives generally prefer clean, dry, and oil-free surfaces for bonding. This usually means cleaning the surface with a solvent, or wiping with a solvent followed by chemical treatment or priming
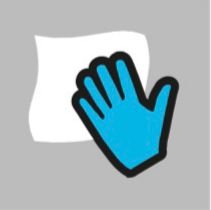
What types of joints are suitable for structural adhesives?
Joints that subject the adhesive to shear, tensile, or compressive forces provide the highest strength. Joints subjected to peel or cleavage forces will have lower bond strength but may still meet your application needs. Additionally, the optimal adhesive bond line thickness typically ranges from 125 to 500 microns. The process of verifying adhesive performance should always include testing sample assemblies to ensure the structural adhesive will deliver adequate performance.
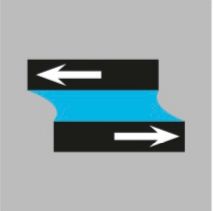
How are structural adhesives used and applied?
Structural adhesives are available in various forms, including low-viscosity liquids, non-sag pastes, one- and two-part formulations, and various working times and packaging shapes. Most two-part adhesives are available in bulk containers and practical mixing dispensers.
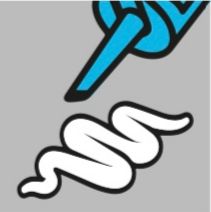
What general properties exist among different types of structural adhesives?
All structural adhesives have a minimum shear strength of 7 MPa to aluminum. However, different adhesives exhibit various characteristics:
Two-part epoxy adhesives provide the highest strength and performance, along with excellent heat, solvent, and weather resistance. They bond well to metals, wood, and concrete but require clean, roughened surfaces for maximum bond strength.
Two-part acrylic adhesives offer excellent bonding and durability, slightly less than epoxy. They are user-friendly, cure quickly, tolerate oily or unprepared surfaces, and can bond all plastics. New formulations of acrylic adhesives are room-temperature stable and have a longer shelf life with less odor compared to traditional acrylics.
Two-part polyurethane adhesives have a relatively long cure time, providing excellent impact resistance and good bonding to most plastics, wood, concrete, and rubber, but typically have lower resistance to solvents and high temperatures. Uncured adhesive is moisture-sensitive and may not fully cure.
Cyanoacrylate adhesives (super glues) are low-viscosity, one-part liquids that cure rapidly in the presence of air and moisture. They bond well to plastics, metals, and rubbers, and can bond low-energy plastics and elastomers with primers. Compared to structural adhesives, they are less flexible and have lower peel and impact resistance, making them suitable for bonding small objects and parts.
Anaerobic adhesives are one-part adhesives that cure in the absence of air and contact with metal. They provide good chemical, vibration, and shock resistance in joints, filling gaps between surfaces or threads effectively for leak and corrosion protection.
PUR adhesives (reactive polyurethane adhesives) are one-part adhesives made from urethane polymers with isocyanate-based chemicals. They cure similarly to hot melts but develop bonding strengths comparable to structural adhesives in the presence of moisture. They can achieve a maximum shear strength of 7 MPa within 24-48 hours and are flexible and resistant to high temperatures and most solvents, commonly used where at least one substrate contains or transmits moisture (e.g., automotive, packaging, woodworking, printing, shoe manufacturing, and construction industries).
